Recently Lee Kirk announced that she had “Molds, Mats, Moulds, Flongs” for sale on Etsy. I didn’t know the word flong so I took a look. According to wikipedia
Flong is a term used in relief printing (also called a stereo mould), which refers to an intermediate step in making of a stereo plate typically used in a rotary press though not exclusively. The process was called Stereotyping.
Invented in Lyon in 1829 by the French printer Claude Genoux, a flong was a papier-mâché mould made with the aid of heat and pressure of a set forme of type. After placing it in a casting box, a thin replica of the original (metal) type (and illustrations) would be cast against it all in one piece. A limited number of duplicate casts could be made from one flong. The back shaved stereo plate would be attached to a press cylinder or honeycomb base and allow the original undamaged type to be distributed or recycled. The stereotypes could be stored for repeat editions in much less space than standing forms.
A further improvement to the technique was made in 1893, when the dry flong replaced the wet flong. More recently, flongs have been made of phenolic resin boards (perhaps also plastic and rubber) and are still used in places to cast rubber stamp sheets instead of type metal stereos, the last commercial use is certain types of rubber relief printing mats (sheets) for flexo printing. They remained widely in use until the invention of offset lithography in the late 19th century led to rotary presses being mostly replaced by the new technology.
The word is derived from the French flan; or the Latin word “flana”.
Here’s one of the flongs Lee is selling, from 1929.
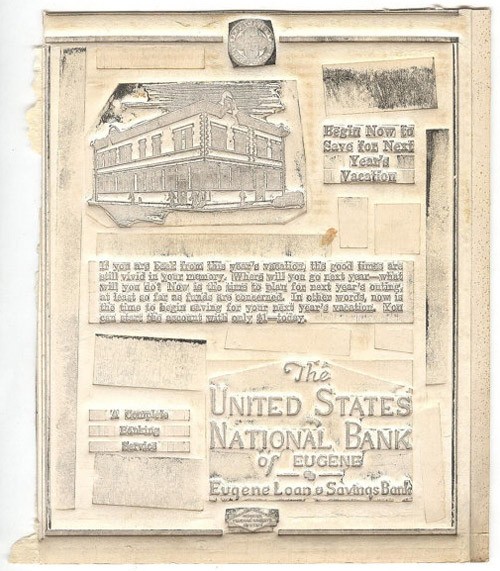